Accurate level measurements
Level transmitters are an essential part of many processes, from food production to wastewater treatment.
It is essential that the information they provide is accurate because if tank levels are too low, pump damage can occur; or if tank levels are too high, vessels can overflow, causing product loss, safety issues and environmental problems.
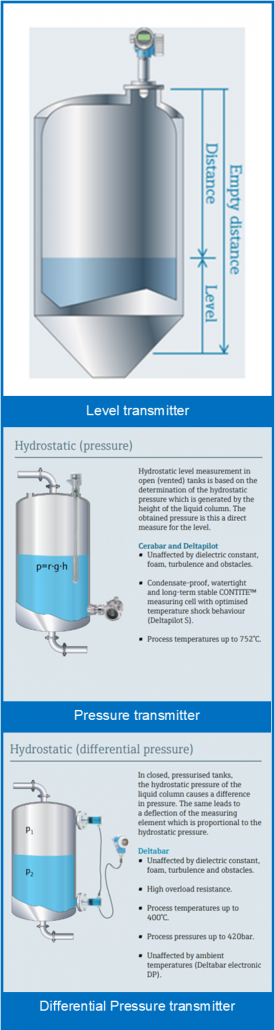
Image source: Endress & Hauser
Some liquids are very easy to measure. Clean water, for example, is easy for almost any level transmitter to measure.
A radar device, for example, would measure the level by calculating the distance between the antenna and the product surface by emitting microwaves. But some fluids, like those that produce foam, need special attention to get an accurate measurement.
The main problem that arises is that foams are often not consistent, and the thickness and density will vary with changing process conditions. In these cases, the level signal can jump between the surface of the foam and the true liquid level. In some circumstances the microwave energy may even be entirely absorbed by the foam and no usable echo is returned to the transmitter resulting in a loss of level control.
This is where pressure transmitters can provide an excellent alternative
Hydrostatic pressure transmitters can provide an accurate, reliable level measurement of the liquid inside a tank or vessel while ignoring the foam. The pressure transmitter is installed near the bottom of the tank with the instrument’s measuring cell touching the liquid. Using the mass of the stationary liquid above it and the liquid’s known density, the sensor is able to calculate an accurate level.
The pressure sensor can make an accurate level measurement despite foam because the foam is made up of mostly gas and has little to no effect on the hydrostatic pressure measurement. Also, the only contact with the liquid is at one small point near the bottom of the vessel, so mixers and heating coils don’t interfere with the measurement, either.
Hydrostatic pressure sensors work best when the liquid being measured maintains a constant density. If the density changes due to temperature or composition, there will be a comparable fluctuation in the level output as the actual level stays the same. Fortunately, this minor setback can be overcome by using two pressure sensors and measuring the differential pressure.
To do this, two independent pressure sensors are submerged at different levels in a fluid. The density is then calculated based on the changing differential pressure.
EAS’ expertise and experience in installing level transmitters means we can assist you with working out the best solution for measuring liquid levels for your plant and processes to ensure you have the accurate results you need.
Why not get in touch with the team today on 07 834 0505 or [email protected]
Leave a Reply
Want to join the discussion?Feel free to contribute!