Essentially, everything that plugs in has the potential to pose a threat to your staff if not maintained or used correctly.
Under the New Zealand Fire Safety Evacuation Procedures and Evacuation Schemes Regulations 2018 it is now mandatory to perform regular checks on electrical equipment to minimise these risks. How regular these checks need to be depends greatly on the environment the equipment is being used in. For example, equipment used in manufacturing environments requires 6 monthly checks while portable equipment or equipment used in an office may only require an annual check.
The types off equipment you may need to test includes:
- power boards and extension cords
- cooking equipment
- cleaning equipment
- power tools
- office equipment
- fans and heaters
Some of the key checks that need to be performed include
Checking Cords
Cords, including extension cords, can become worn over time. Frayed, cracked or damaged cords are dangerous and risk causing fires or electrical shocks. Cords need to be checked regularly to ensure the cord itself in in good condition, the cable entry and anchor points into plugs and sockets are secure and no wires are exposed.
It should also be remembered that extension cords should only be used as a temporary solution. If a permanent power source is required in a specific location, EAS can assist with installing a safe permanent solution.
Multi-boxes
Overloaded multi boxes are a common cause of fire in New Zealand.
Multi-boxes due to their portability means they can be easily damaged by dropping or becoming trapped between office furniture. As the multi-box ages, contacts can stretch causing a bad connection between the plug and outlets, this can result in a hotspot which may lead to an electrical fire.
While multi-boxes can provide a handy solution to increased electrical outlets, it is vital that these are not overloaded and if your office set-up is unlikely to change, investing in installing more permanent powerpoints makes sense from a safety perspective and to create a tidier work environment.
Other risk factors
Appliances that are used intermittently throughout the day by various employees can provide a potential hazard. No one person takes responsibility for ensuring these are turned off when unattended. This can be particularly common in your lunchroom.
EAS recently installed a timer on a toasted sandwich maker in a client’s lunchroom to ensure that it would automatically switch off after 20 minutes. An easy safe solution for all.
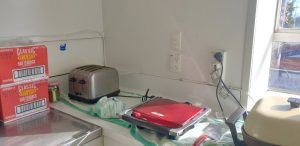
Toasted sandwich maker frequently left on creating a potential fire risk.
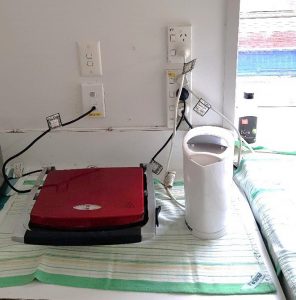
Toasted sandwich maker wired into a timer so it will automatically switch off after 20 minutes.
With the holiday period fast approaching, now is a great time to make sure your testing and tagging is up-to-date to ensure the safety of your site while staff are away on holiday. Why not give the EAS team a call on 07 834 0505 to book your job today.